Thermoacoustic Refrigeration
Garrett and Hofler (1992) indicates that two recent developments are responsible for the new em in cold storage until the beginning of the twenty-first century. The most significant of these is the international Treaty (the signing of the Montreal Protocol on production and consumption of CFCs, which were depleting the ozone layer. The second event was the opening of the " high-temperature " superconductors and the development of high speed and high density electronic circuits that require active cooling and, consequently, a new approach to cooling or thermoacoustic refrigeration, which was first discovered Wheatley and others (1993) in August 1983. The simplicity of equipment involved in thermoacoustic machines best appreciated by studying a specific example. In the mid-1990s, S.L. Garrett and his colleagues at the naval Postgraduate school in Monterey, California) developed two thermoacoustic refrigerators for the space Shuttle. The first was designed for the cooling of electronic components, and the second was intended to replace the refrigerator / freezer unit, used to store the blood and urine, of the astronauts involved in biomedical experiments . Thermoacoustic refrigeration is considered new technologies, achievements cooling without the need for refrigerants.
The basic mechanism is very simple and effective. Loudspeaker creates sound in a hollow tube that is filled with conventional gas. In fact, thermoacoustic refrigeration uses a high-density sound waves to transfer heat from the thermoacoustic effect (i.e.. the acoustic energy). Therefore, the working body in this system is acoustically driven gas. The process uses a standing acoustic waves in a closed cavity to create mechanical compression and expansion of the working fluid (gas, in this case)required for cooling cycle. The technique has the potential for high efficiency of work without the need for cooling liquids or mechanical moving parts. These factors make the concept of amenable miniaturization on chip-scale dimensions for thermal management of electronic components.
Interaction between acoustics and thermodynamics was known ever since the dispute between Newton and Laplace about the speed of sound is determined by the adiabatic or isothermal compressibility of air. Today the efficiency of thermoacoustic refrigerators 20РІР‚30% lower than their vapor compression refrigeration. Part of that reduction of capacity due to own irreversibilities of thermoacoustic heat transport process. These inherent irreversibilities also favorable aspects of the cycle, because they do for mechanical simplicity, with few or no moving parts. A large part of the inefficiency of the current thermoacoustic refrigeration, simply because of the technical immaturity. Over time, improvements in heat exchangers and other subsystems must reduce the gap. It is also likely that the efficiency in many applications will improve only because thermoacoustic refrigerators are well suited for a proportional control. You can easily and continuously monitor the cooling capacity of thermoacoustic refrigerator so that the output can be adjusted accurately for different load conditions. This can lead to higher efficiency than conventional vapor compression chillers that have a permanent displacement compressors and so can only binary (on/off) control. Proportional control allows to avoid losses due to start-up jumps in conventional compressors and reduces inefficiency of heat exchangers, as such systems can work for less expansion gaps between the coolant and the heat load.
The research focus of the Thermoacoustics Laboratory in ARL at Pennsylvania state University in cooperation with the Los Alamos national Laboratory Research is to study acoustically driven heat transport. Their objectives include the improvement of the understanding of the fundamental thermoacoustic processes and development of new thermoacoustic refrigerators and thermal engines of increased power density, temperature span, and efficiency, and commercialization of these devices. The laboratory provides the infrastructure to support research on the main processes necessary for the understanding of this new ecologically friendly technologies of cooling. This feature also supports manufacturing and tests that are necessary for the production of the full, full working prototype of cooling systems for military and commercial applications, such as food refrigerators/freezers and air conditioners. Their prototypes were delivered to the space Shuttle and used for cooling radar electronics aboard the U.S. Navy warship.B Thermoacoustic refrigerators with cooling powers, ranging from a few watts to chillers with a refrigerating capacity exceeding 10 kW are currently in operation or under construction. Fig. 3.70a shows thermoacoustic refrigerator, developed by the Laboratory and rapid start-up of small refrigerator in Fig. 3.70b. Although thermoacoustic refrigerators was not put into production, but are considered to be still under development, it is known that they can be used for any type of cooling. Conventional, single-stage, electric wing mirror, thermoacoustic refrigerators can reach the cold side temperature range from two thirds to three quarters of the environment, so they are not very well suited for applications cryogenic below goldfish40V. However, thermoacoustically driven pulse-tube refrigerators can get to cryogenic temperatures required for liquefying air or gas. In their early stages of commercial, they probably will be limited to niche applications, such as in military systems, which are required to work indoors and food merchandising, where toxicity is an important issue. As a global environmental obligations and laws and amendments, which become significant, it can be expected that the volume of thermoacoustic applications for expansion, both within countries and emerging markets. 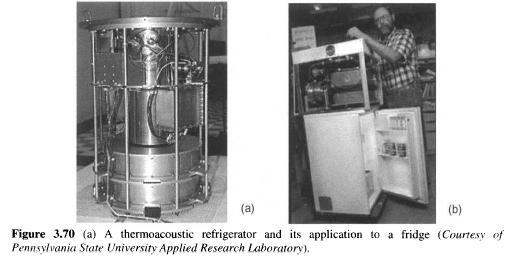 ..
|